Team ACRV, Winner of the Amazon Robotics Challenge 2017
페이지 정보
작성일2017/11/13 11:17 Hit2,264Team ACRV, Winner of the Amazon Robotics Challenge 2017
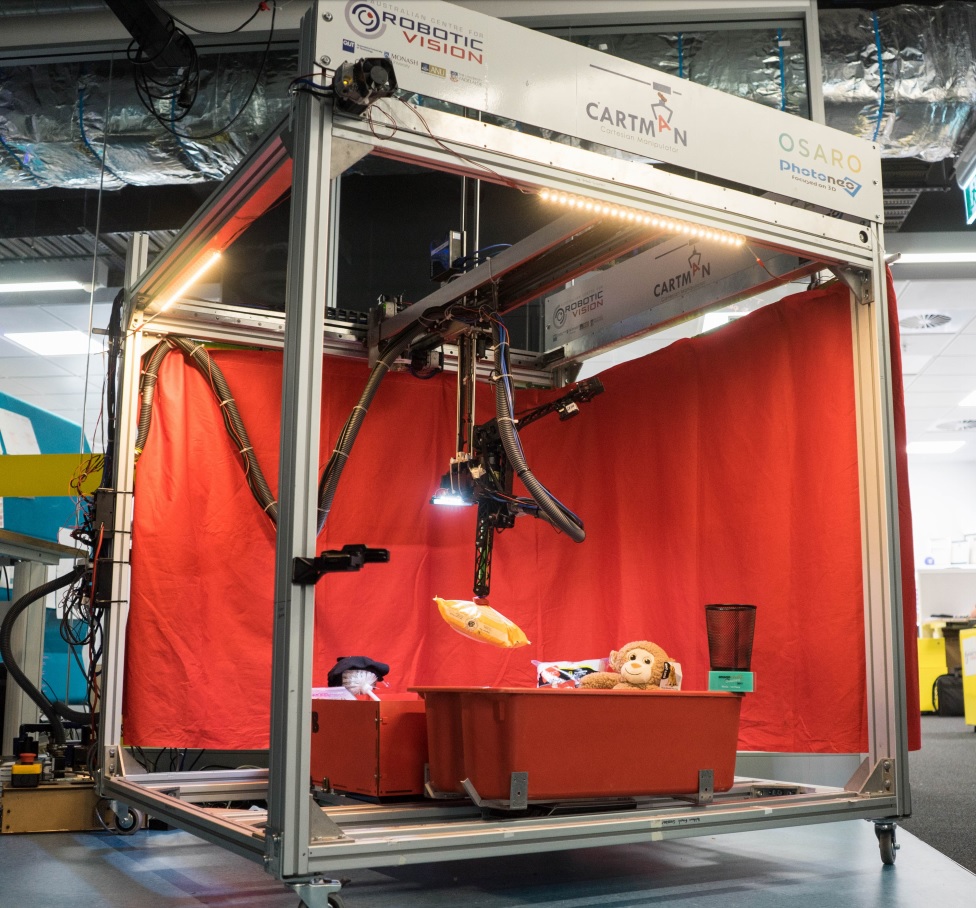
We had a short interview with Team ACRV (Australian Centre for Robotic Vision), the winner of the Amazon Robotics Challenge (ARC), which was held in Japan on July 27th to 30th.
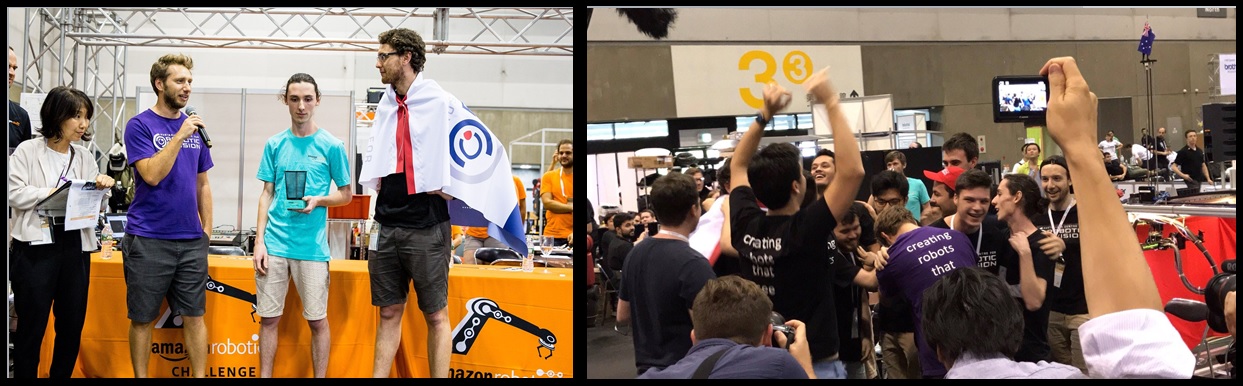
Team ACRV the winner of this year’s Amazon Robotics Challenge (ARC), which was held in Japan on July 27th to 30th, did not become a winner overnight. Thanks to their countless days of hard work and hands on experience hands, their fearless plunge to change brought them to victory.
Q : Is there any reason why you switched to Cartesian from Manipulator?
Juxi: After our experience last year with motion planning and robot arms, we looked for alternatives to make the planning problem simpler. This and the rule changes, which allowed horizontal shelving were the major deacons for us to try a cartesian setup. It also allowed us to have full control of the software and hardware stack ourselves.
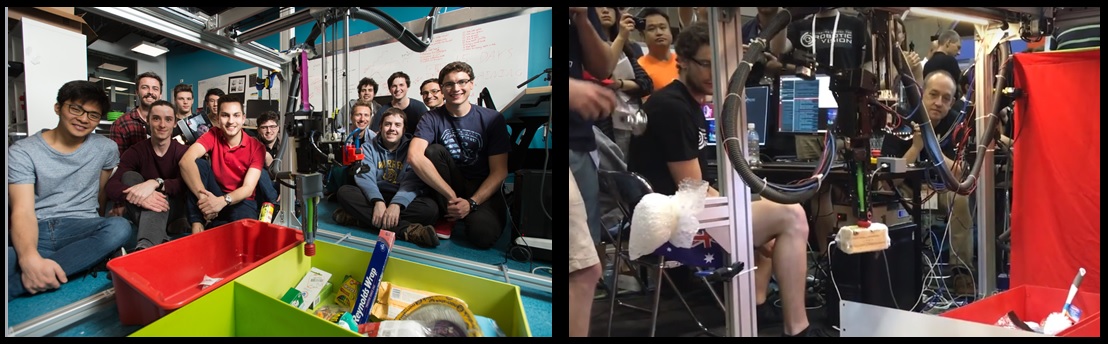
Q : Why did you choose to use our Dynamixels for the ARC mission?
Juxi: We had prior experience with Dynamixels and we had spec-ed out cartman before with these. Accuracy and torque are definitely reasons. We use 3 motors for the XYZ, plus another 3 on the wrist. In addition smaller motors were used for the bending of the suction and the closing of the gripper.
Matthew: For the wrist joint I chose to use three Dynamixel Pro as they had the exact specs I was after (mainly torque). The ease of integration was also a nice bonus.
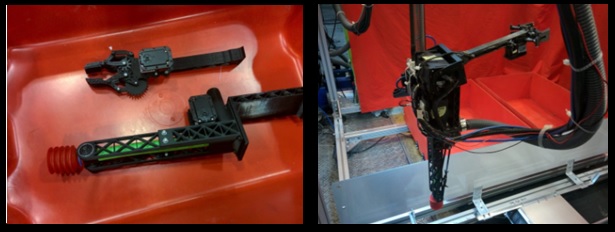
Q. We heard that you faced a problem during the competition. How did you solve it and become the winner?
Juxi: As in every competition there is multiple problems :) It’s how you deal with that, which differentiates the teams. As we had fully developed our H/W and S/W stack we knew how to fix all the smaller problems rather quickly and efficiently.
The big issue was that we ran into the shelf and broke a part, we solved that by 3d printing spare parts, plus setting our limits better :)
Q. What applications will be used in the future? (we saw the fruit harvest in your application video :-) )
Juxi: That’s a good question. We are talking with various interested parties. There are a few interesting research projects going on here, including fruit harvesting. There is the opportunity to spin this tech out and get some industry coverage, firstly logistics and warehousing but other areas such as recycling, restocking or supermarkets, etc. exist as well.
From a research point of view, we are interested in creating robust object grasping and manipulation theory and systems, from industrial settings all the way to domestic.
For more pictures and videos of the competition, click here.
Available Link :
Mechanical Design of a Cartesian Manipulator for Warehouse Pick and Place
https://arxiv.org/pdf/1710.00967.pdf
AR Challenge
https://www.amazonrobotics.com/#/roboticschallenge
(Images courtesy of robonews.net and Team ACRV)
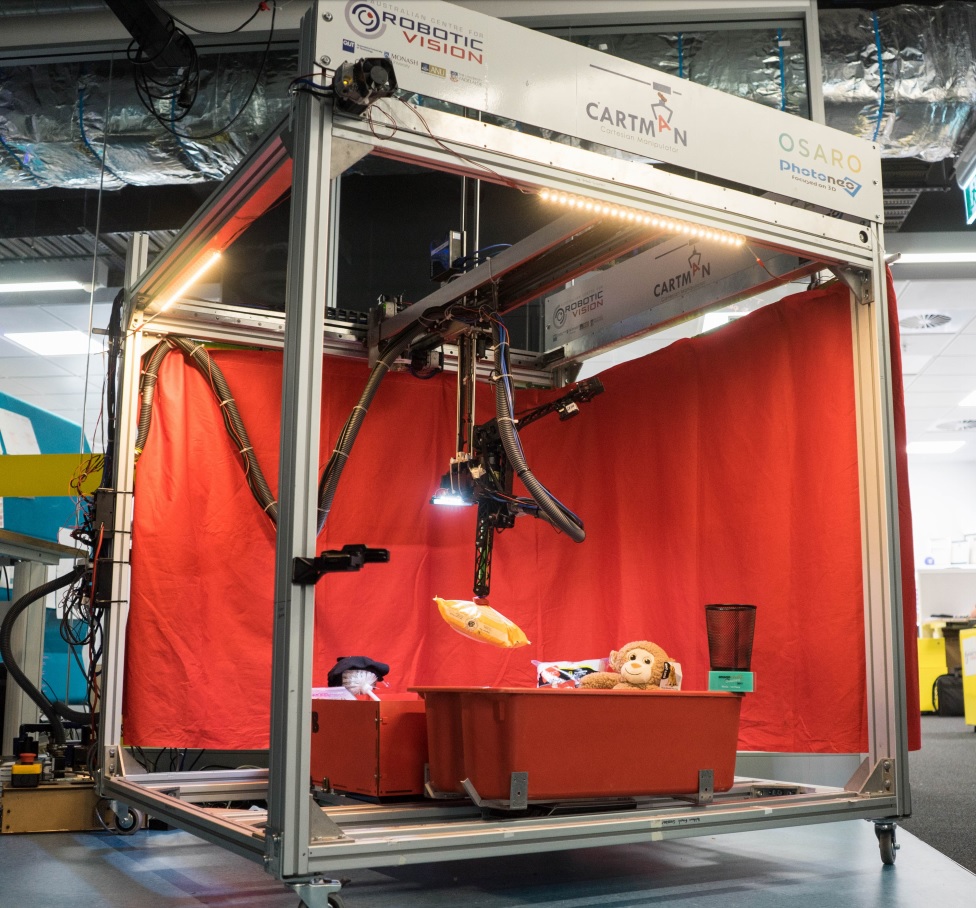
We had a short interview with Team ACRV (Australian Centre for Robotic Vision), the winner of the Amazon Robotics Challenge (ARC), which was held in Japan on July 27th to 30th.
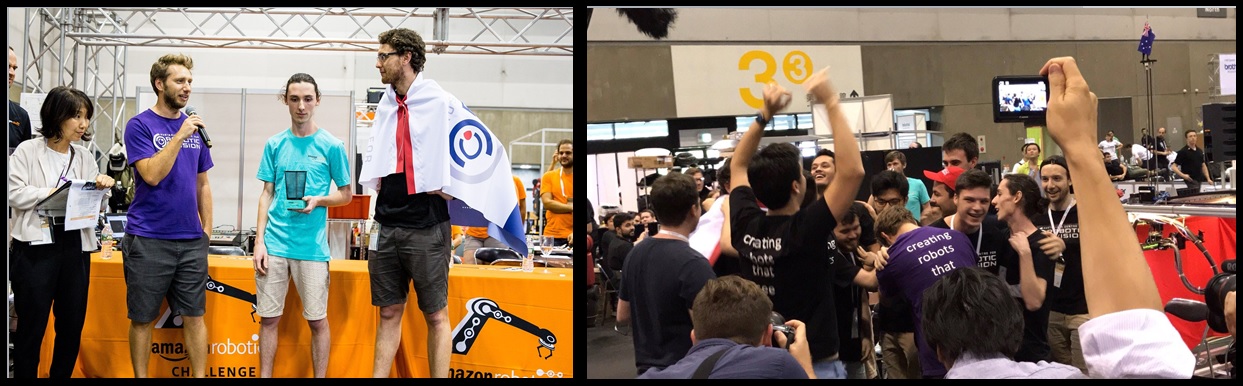
Team ACRV the winner of this year’s Amazon Robotics Challenge (ARC), which was held in Japan on July 27th to 30th, did not become a winner overnight. Thanks to their countless days of hard work and hands on experience hands, their fearless plunge to change brought them to victory.
Q : Is there any reason why you switched to Cartesian from Manipulator?
Juxi: After our experience last year with motion planning and robot arms, we looked for alternatives to make the planning problem simpler. This and the rule changes, which allowed horizontal shelving were the major deacons for us to try a cartesian setup. It also allowed us to have full control of the software and hardware stack ourselves.
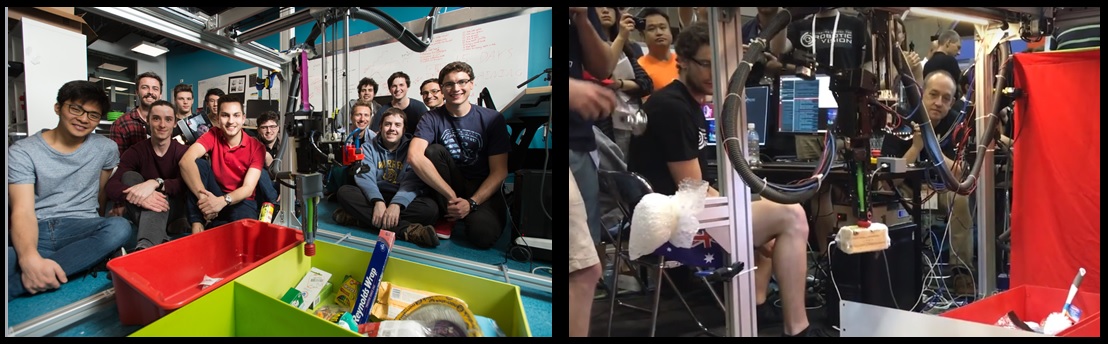
Q : Why did you choose to use our Dynamixels for the ARC mission?
Juxi: We had prior experience with Dynamixels and we had spec-ed out cartman before with these. Accuracy and torque are definitely reasons. We use 3 motors for the XYZ, plus another 3 on the wrist. In addition smaller motors were used for the bending of the suction and the closing of the gripper.
Matthew: For the wrist joint I chose to use three Dynamixel Pro as they had the exact specs I was after (mainly torque). The ease of integration was also a nice bonus.
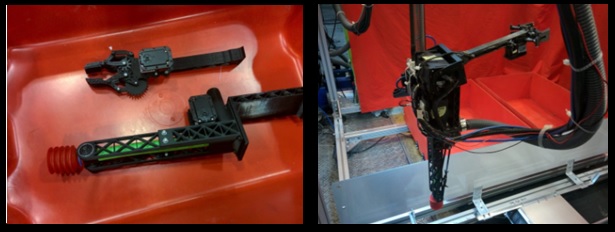
Q. We heard that you faced a problem during the competition. How did you solve it and become the winner?
Juxi: As in every competition there is multiple problems :) It’s how you deal with that, which differentiates the teams. As we had fully developed our H/W and S/W stack we knew how to fix all the smaller problems rather quickly and efficiently.
The big issue was that we ran into the shelf and broke a part, we solved that by 3d printing spare parts, plus setting our limits better :)
Q. What applications will be used in the future? (we saw the fruit harvest in your application video :-) )
Juxi: That’s a good question. We are talking with various interested parties. There are a few interesting research projects going on here, including fruit harvesting. There is the opportunity to spin this tech out and get some industry coverage, firstly logistics and warehousing but other areas such as recycling, restocking or supermarkets, etc. exist as well.
From a research point of view, we are interested in creating robust object grasping and manipulation theory and systems, from industrial settings all the way to domestic.
For more pictures and videos of the competition, click here.
Available Link :
Mechanical Design of a Cartesian Manipulator for Warehouse Pick and Place
https://arxiv.org/pdf/1710.00967.pdf
AR Challenge
https://www.amazonrobotics.com/#/roboticschallenge
(Images courtesy of robonews.net and Team ACRV)